Corrosion resistance
The density of aluminum profile is only 2.7g/cm3, which is about 1/3 of the density of steel, copper or brass (7.83g/cm3, 8.93g/cm3, respectively). Under most environmental conditions, including air, water (or salt water), petrochemicals and many chemical systems, aluminum can show excellent corrosion resistance.
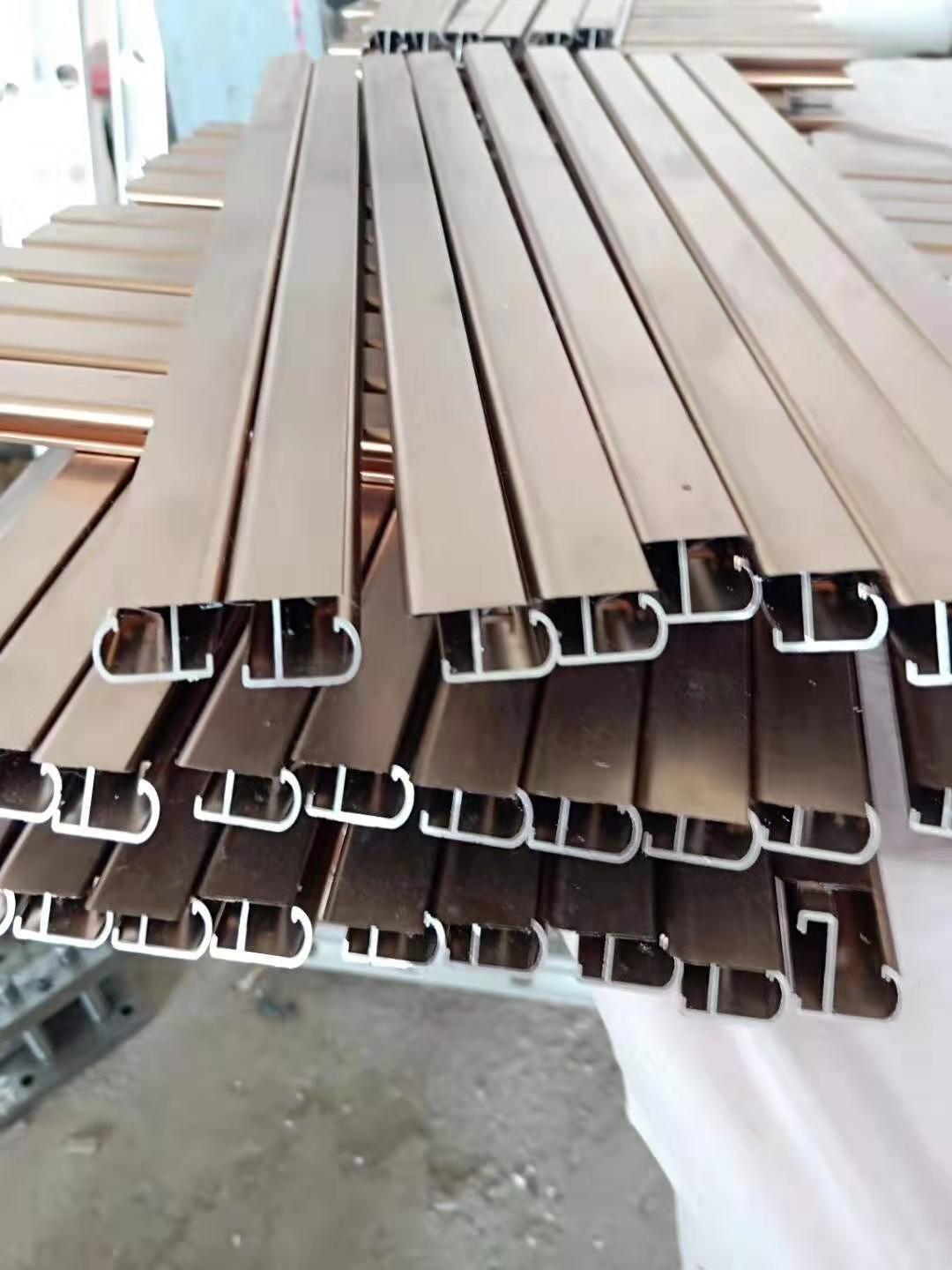
Conductivity
Anodized extruded aluminium alloy frame is often selected because of its excellent electrical conductivity. On the basis of equal weight, the conductivity of aluminum is close to 1/2 of that of copper.
Thermal conductivity
The thermal conductivity of aluminum alloy is about 50-60% of copper, which is beneficial to the manufacture of heat exchangers, evaporators, heating appliances, cooking utensils, and automobile cylinder heads and radiators.
Non-ferromagnetic
Aluminum profiles are non-ferromagnetic, which is an important feature for the electrical and electronic industries. Aluminum profiles are not spontaneously combustible, which is important for applications involving handling or contact with flammable and explosive materials.
Machinability
The workability of the Anodised extruded aluminium alloy frame is excellent. In various deformed aluminum alloys and cast aluminum alloys, as well as in the various states that these alloys have after being produced, the machining characteristics vary considerably, which requires special machine tools or technology.
Formability
The specific tensile strength, yield strength, ductility and corresponding work hardening rate dominate the change in allowable deformation.